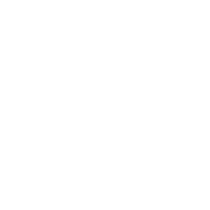
In this episode, Bill Bellows and Andrew Stotz dive further into acceptability versus desirability in the quality world. Is it enough that something is "good" - meets requirements - or do you need to focus on degrees of "good"? How can you tell the difference?
TRANSCRIPT
0:00:02.5 Andrew Stotz: My name is Andrew Stotz, and I'll be your host as we dive deeper into the teachings of Dr. W Edwards Deming. Today, I'm continuing my discussion with Bill Bellows, who has spent 31 years helping people apply Dr. Deming's ideas to become aware of how their thinking is holding them back from their biggest opportunities. Episode, today is episode eight, Beyond Looking Good. Bill, take it away.
0:00:25.4 Bill Bellows: Hi, Andrew. How are you doing?
0:00:29.1 AS: Beyond looking good. So beyond my good looks, that's what you're saying. Okay.
0:00:33.6 BB: No, but it's funny, this beyond looking good and so I could say, Andrew, how you feeling? Oh, I'm feeling good. Right? I'm feeling good. So we have this, and that's part of why I think is funny is how are things? Things are good, things are good.
0:00:49.3 AS: Looking good.
0:00:51.0 BB: And that's what I find is, I mean, and it's not that people are necessarily honest, but when somebody says how was your day? Good. Or it could be the extreme other, and we won't use any foul language, but it's like, but I find it's just a very common, how are you feeling? Oh, I'm feeling good. Or I could say, great, which is better than good. So anyway, so I'm gonna pick up on, well first say that a heavy focus of this series, Misunderstanding Quality, is for you, quality professionals out there around the world that are excited by Deming's work, learning about Deming's work, trying to bring Dr. Deming's ideas to your organization in your quality function.
0:01:41.6 BB: Or it could be, you're elsewhere in the organization and you believe that...you're inspired to realize that there's something about how quality is managed in your organization, whether you're in design or manufacturing, which is inhibiting what you might want otherwise to do. And what I'm hoping is that the examples and concepts presented here can help you, one, absorb the ideas yourself, begin to absorb them, eventually explain them to people at work. At least once a month I'm contacted by someone listening to the podcast who says, hey, they wanna connect with me on LinkedIn, and then quite often I reach out to them and ideally end up in a conversation with them to find out more about what they're trying to do.
0:02:38.7 BB: But what I'm hoping is that this fundamental information, knowledge, wisdom is useful to you and personally learning, but then depending on what you wanna do with it, you have to engage others. And that's why I've been encouraging, and this is what I do with people I mentor, is you have to develop the ability to explain it to others. 'Cause you can't be the only one talking about these differences. You're gonna drive your coworkers nuts. You might get in a jam where somebody's confused by what you're trying to do, and you need help, or you need help in implementation, help in explaining.
0:03:17.6 BB: So I'm gonna go back to acceptability and desirability. And I was in the Finland, the Netherlands and the Sweden about a month ago with friends in each of those countries. And what came up was, again, this acceptability/desirability and that contrast. So acceptability again, as a reminder is, there's no need to know where we are within the requirements. It is absolutely good. All we know is that it meets requirements for whatever the requirements are. It is you're comfortable with good versus bad. I was talking with somebody, some clients today and we were talking about, pass versus fail. And I said, 'cause it's really a pass. Acceptability is a pass-fail system. And what does passing mean?
0:04:17.5 BB: Passing means not failing. It's like, years ago when I was a summer student working for this jet engine company in Connecticut and got together for beers one Friday night with a couple of the executives, and there were a couple of us summer interns there with these directors. Yeah. Senior directors. And one of the senior directors says to us, says, so what's the difference between business and crime? And we're like, this and this and this and this. And I don't know what our answers were, but we. And finally one of them said, no, no, no, no, no, no. He said, the basic difference is crime's illegal.
0:05:03.0 BB: So you end up with what is bad, what is bad is what's not good. And what is good, good is what's not bad. And so what is passing? Passing is not failing. And so when I was explaining to somebody today I was asking him, what's the letter grade? What letter grade? In fact, I asked a very senior NASA executive this question once. What letter grade do they expect for everything they buy that put into their missions? And he said, A plus. And I said, A plus is not the requirement. He said, what's the requirement? I said, D minus. And he is like, nah, it's not D minus. I said, your procurement system is based on things being good or things being bad. He said, yep.
0:05:45.7 BB: I said, well, what is good but passing? Right. Good is not... Good is... To be good is to not be bad, to pass is to not fail. What is crime? What is crime is what's illegal versus legal. It's one or the other. We talked once on the previous podcast about Kepner-Tregoe problem solving, decision making. And part of decision making I mentioned is you come up with a bunch of characteristics of a decision. You're buying a house and you want it to be one story, three bedrooms, two bathrooms, whatever it is. And you put down all the requirements and then you ask for each of those requirements. Is it a must or a want? And a must is yes or no. It has it or it doesn't. So it must have three bedrooms, must be one story. The must could be must be under a million dollars or whatever the number is.
0:06:53.5 BB: And then you get into, well, is that really a must or is that a high weighted want? For our daughter, Allison, I remember taking her out to buy a bike for her birthday one year and she said, well, how much can we spend? And I said, $200. So, what did she say, Andrew? "What if it's 201?" Well, then you get into, well, is that a must or a high weighted want? You know what I say? Depends on how much money's in your wallet. If you don't have $201, it is a must if you're...
0:07:34.7 AS: I thought she was gonna say, if I can get it for 150, can I keep the 50 bucks?
0:07:41.3 BB: But that's it. So acceptability is like treating it as a must. It is absolute. It has to be three bedrooms. And then what is desirability? Desirability is the lower the cost, the better, the higher the performance, the better. And so acceptability is absolute, it is good versus bad. Desirability there's relativeness. And the next thing I wanna say is why should we be interested in desirability? Which also based on what we've talked about before, is to be appreciative of desirability in regard to the Dr. Deming's Red Bead Experiment. Deming Red Bead Experiment, we had red beads and white beads the customer wanted white beads. And then one of the things we looked at was, if all the red beads are gone, can we still improve?
0:08:46.1 BB: And then people would say, well, we can make the white beads faster, we can make them cheaper, but can we make the white beads better? And the huge blind spot and asking that question to audiences on a regular basis is, they get stuck. Well, then we got into, well, what if there's variation in the white beads? So part of desirability is that there's variation in good. And that allows us to go beyond just being good to better. But what is better than? Well, better than is, I mean, what would be better for the organization would be a better appreciation of the white bead variation. One, could prevent red beads from happening in the first place. And so why do we have a gas gauge that goes anywhere from E to full? It allows us to watch the gauge go down and go down and go down.
0:09:39.7 BB: What does that? It's watching variation in good and then getting gas before it runs out. So if we use a run chart and monitor vacuum level in a braze oven if we're monitoring something on a variable way, not just saying it's good or it's bad, that allows us to see trouble coming before it happens. We could use that information to create a control chart and go one step further. And so relative to a given characteristic, what we're doing is trying to prevent non-conformances, trying to prevent bad from happening by monitoring what is good. What we can also do and what I shared is with appreciation of Dr. Taguchi's insights, the idea that the closer we are to that ideal value so when we're at home cutting the piece of wood really close to that line, why do we do that?
0:10:33.7 BB: Because at home we have to get those pieces of wood together and they're not quite square or straight, then that's extra work over there. So those are two aspects of the value proposition for desirability. And then I wanted to mention is, our son is a handyman and a pet sitter. And he is self-employed in both. And the handyman stuff involves and sometimes it involves woodworking. And recently he's doing some work in our house and some really cool stuff. So he experiments in our house, which is great for us. He also experiments in our daughter's condo. So there's great opportunities for him to practice doing something. So he was cutting some long pieces of wood and they weren't, he was very frustrated. They weren't coming out straight. So we called a friend who's a master craftsman over, and he gave us both a lesson on how to, how desirability, how to get a really straight cut, not just anywhere within spec, but you need a really straight cut so they fit together well.
0:11:38.6 BB: Well, this carpenter friend, Alex, shared with me a while ago, years ago, what it's like in the construction industry. 'Cause I explained to him acceptability, desirability, focusing on the target. And in the world of construction, he gets involved, he'll be involved on a team building a multimillion dollar home for six months to a year. And it's not uncommon he's called in to have to deal with everybody else barely meeting requirements. And his job is to go in there and straighten things up because they're not quite right. And that's all this compensation stuff. And that's what with his insights trying to help our son get around that. All right, so, I do wanna share a couple anecdotes from Rocketdyne the world of acceptability and so it was a fun story.
0:12:41.2 BB: I was meeting with a small team and one of them was a senior quality manager and in the quality organization. And he says, you know what the problem is Bill? He says, what's, you know what the problem is? He said, "the problem is the executives VP of quality and as directors are not getting the quality data fast enough." So I said, "well, what data?" And he says, "scrap and rework data. He said, "they're just not getting it fast enough." So I said, "I don't care how fast they get it it's already happened."
[laughter]
0:13:18.9 BB: And I kept saying to him, the speed doesn't matter. And so how many red beads did we have today? Well, we gotta instantly report the number of red beads on a cell phone. No. If you monitor the white bead variation, then that's a means to do that. Also say, when I joined Rocketdyne in 1990, there was a big movement on the space shuttle main engine program. And I don't know what instigated this, but Rocketdyne developed, designed and developed and then produced for many years the space shuttle main engine. I mean the world's first reusable rocket engine. And there was a movement before I got there to change the drawings. And so a set of manufacturing drawings will have a nominal value, let's say 10. And then it might be something must be 10 plus or minus one.
0:14:19.4 BB: And what does that mean in terms of acceptability? It means anything between nine and 11. And then what I learned was they'll say that the number 10, that's the nominal value. And then we have 10 plus or minus one. Well, what matters to the person downstream is not the 10 plus or minus one. What matters to the person downstream is it's gotta be between nine and 11. So no matter what that nominal is, the nominal goes out the window. So there was a movement to get rid of the nominal value. 'Cause now the machinist has to do the math, 10 plus or minus one. Okay? Anything between nine and 11. So we're gonna save you all that trouble and just give you two numbers. The min and the max. And so what is that system? That is a system based on acceptability.
0:15:07.0 BB: And so that was the starting point when I joined. And so what I wanted to add for our listeners, if you're in an organization, this came up recently with one of my clients, and they're talking about the nominal value of that 10. The 10 plus or minus one, or it could be the nominal value is 11 and they'll say 11 plus nothing minus two. And so what does that mean? 11 plus nothing means eleven's the max minus two means nine and 11. So when I saw it doesn't really matter what the nominal value is, 'cause all that's gonna happen is gonna get translated to a minimum and max. And so in this client, they're talking about nominal values, nominal values. And I said, my recommendation is when it comes to desirability, don't say nominal.
0:16:00.3 BB: 'Cause I'm not convinced we use that term the same way. What I would suggest, again, this is for those listening to the podcast on a regular basis, is don't use the word nominal. It's confusing. Use the word target. Say that is the ideal. And the idea, by using the word target, which may not be part of the vocabulary, you can differentiate from nominal, which I find to be confusing and just say that's what we want. I'm gonna give you another fun story relative to acceptability. I was at a supplier conference, so in the room are a couple hundred Rocketdyne suppliers. And the person speaking before me says, and there was some very heavy duty brow beating.
0:16:48.0 BB: And the person ahead of me says, when we give a Rocketdyne employee a job and they sign that it's good, that's their personal warranty, Andrew. That's their personal warranty. So for you suppliers, when you tell us something is good, that's your personal warranty to us. And so that has to be transmitted to your organization. That's personal warranties. We take it seriously. This is the space business, Andrew. So that was going on and there was some heavy duty browbeating. And on the one hand I'm thinking, I wonder what happened recently where somebody said, Andrew, get up there on stage and go browbeat 'em, go browbeat 'em. And so this guy's up there, browbeating, browbeating.
0:17:42.7 AS: We need people to take this serious.
0:17:44.0 BB: Well, this is personal warranty, Andrew. When you say it's good, that's your warranty. So I got up and I told the story of the bowling ball being left in the doorway of the bedroom. And I said, the fact of the matter is, Wilson gave us his personal warranty that the bowling ball was in the bedroom. And just trying to say, 'cause the personal warranty is not a personal warranty of an A plus Andrew. It's not a personal warranty. It's a personal warranty that it's good and what is good, Andrew? Not bad. And so when I hear this talk of personal warranty, it's like it's not all that it's cracked up to be. When you start to look at what is good is what's not bad.
0:18:36.4 AS: By the way, I have a funny one to share in this one. And that is, every time I start my ethics in finance class with a new batch of fourth year finance students here in Thailand, class starts at 9:00 AM and the students think that the time to arrive is somewhere a little bit before or a little bit after nine. And when they arrive at the class at 9:01 or actually just after 9:00, they find the door is locked.
0:19:12.3 BB: Yeah.
0:19:13.3 AS: And then I leave them outside. And then after about five minutes, I go out after they've built up a group of people out there and I come out and I talk to them. I said just so you know I want you to be on time for my class. Don't tell me about traffic. Don't tell me you're busy. I got a full-time job and I'm working like crazy and I'm here for you. I'm not making much money out of this. So show me the respect and be here on time. They come in, they walk in shame, past all their classmates, and then they sit down and then I lock the door again, and of course another batch comes at about 9:05 or 9:10.
0:19:46.0 AS: And then I do the same. And then I bring them in, and then next week they come and they're all there at 8:58, let's say 8:59, but nobody arrives past 9:00. And then in the following weeks, I never locked a door anymore. Curious how things change. And of course, things start to shift back to that range around it, but it just made me think about what I do in trying to communicate that, whether it's right or wrong or whatever. But I like doing it because I want the students, I wanna set the parameters from the beginning. Like, take it seriously.
0:20:26.4 BB: Oh yeah. I go to a daily meeting and it starts exactly on the hour and it's done exactly. And everybody knows that. And the degree to which things are accomplished and 'cause the whole strategy was to develop a cadence that, yeah, no, that's...
0:20:56.8 AS: And I have a hard time. I want to, with my valuation masterclass bootcamp, which I do have classes at 6:00 PM. I'm generally pretty lenient letting students come in, but there's a part of me that has... I've started locking the room after 6:03 or so, and then I'll unlock it five minutes, 10 minutes later and let a few people that are... But I've had some questions in my mind as to whether I should just be hard line and say, it starts at 6:00, if you don't make it, see you next time. Now we also record it so they can watch it. But I don't know, I haven't really figured out whether I should be that tough or not.
0:21:35.0 BB: Yeah. And that's what it comes down to. I think depending on the environment, there could be, I mean, it's about synchronizing watches, right?
0:21:48.9 AS: Well, yeah. And the other thing that you could say is that, well, Andrew, come on if you understand variation, then you understand that there's gonna be some people that are gonna be late, and there's gonna be some people that are gonna be early. You set the target at 6:00 PM what else would you expect? But I guess what I'm thinking is, if for a student they should be thinking, I need to shift my target to be 8:00, sorry, 5:55 if the meeting's at 6:00, that way I could be a little bit late, you know?
0:22:16.2 BB: Exactly.
0:22:16.7 AS: And it's same concept, it's just that shifting that target. So maybe I need to start working on that one.
0:22:25.3 BB: No and it's respect for the other 15 people in the meeting that... you know, and this idea that we are... This meeting is designed for this reason, but it has to fit the work. And, yeah, I mean, so is that necessary for a college class? Again, I mean, if it depends on how much you wanna squeeze in. And five minutes if you're trying to get a whole bunch in and develop a cadence, then, yeah.
0:23:07.6 AS: Well, it also depends. What are you teaching.
0:23:11.4 BB: Exactly.
0:23:12.5 AS: In my Valuation Masterclass about valuing companies, I've decided I'm not teaching Excel. You can go somewhere else and get that, and people ask me for it, and I let them use my Excel model that I've created, but I've just decided that's not what I'm gonna teach. And so in this case, with being an ethics class, I think it is probably important to teach about the importance of time and understanding that. And so for that, but for the bootcamp, Valuation Masterclass Bootcamp, I am trying to teach discipline and helping young people realize you gotta deliver. And so that's it. By the way you're looking good, Bill. So let us summarize beyond looking good. How would you like people to... What would you like them to take away from our discussion on this topic?
0:24:07.3 BB: It goes, this is...I mean, we started off this whole series talking about quality and the eight dimensions of quality and the book and the article by David Garvin of the Harvard Business School. So to first introduce in this series called Misunderstanding Quality, that there are dimensions of quality. And amongst those dimensions were capacity and reliability and repairability. And one was aesthetics, and one was a sense of a reputation that through everything else, you're developing a reputation. Well, one of them was acceptability, and that then was the inspiration to get into the contrast between acceptability and desirability.
0:25:05.6 BB: And there's a lot to that. And so what I found in the beginning I had a little bit in mind based on some things I've seen. And then the more I researched it, the more I saw and what I wanna get into next time is, and these are questions I was asking people in the trip to Europe is, first is, can acceptability - a focus on acceptability explain the incredible reliability of Toyota products? At least that I have experienced. Can you explain that with acceptability? And I don't think so. Next, okay, I'll go back to my notes here.
0:25:57.7 BB: Next is, does your organization, again, for those calling in, the better you understand this distinction between acceptability and desirability. Does your organization distinguish those? Does your quality system... Is your quality system based on acceptability? Does it have acceptability and desirability? That is a question for our audience. What I want to get into next time is, and I think I've mentioned this before, I've read much a great deal about Lean. I've gone to Lean conferences. I've written plenty of articles for the Lean Management Journal involving reading articles and commenting on them. Everything I see within Lean is acceptability. I don't see any mention of desirability. Six Sigma quality is that we wanna have 3.4 defects per million. There's no mention in acceptability, either explicitly or implicitly to this difference between acceptability and desirability nor in Lean.
0:27:04.9 AS: Sorry, can you clarify that for just a second? Okay. So you said Lean was one and Six Sigma was the other, which was focused on which?
0:27:13.4 BB: Well, what I'm saying is that I don't see explicitly... I don't see a call out in the Lean literature a conversation about acceptability and desirability. What I see is plenty of evidence of an acceptability-based quality mindset in Lean, in Six Sigma quality, in Lean Six Sigma, in Operational Excellence, in the Toyota Production System is what I see is a heavy emphasis directly about things being good versus bad. I don't see any inference to desirability that there's something beyond good in that system.
0:28:06.4 BB: And that's what I've been wanting to point out, is I think Dr. Deming's work is unique in its appreciation of that distinction in explaining the difference and the value of understanding when acceptability makes sense, when desirability makes sense. And that's what this whole Misunderstanding Quality series, a big part that I'm trying to introduce through my experiences is, if you're interested in moving your organization or just your personal awareness beyond a good mindset into continual improvement, that's what I'm trying to bring about in this series.
0:28:50.5 AS: Fantastic.
0:28:50.9 BB: That's my story, Andrew, and I'm sticking to it.
0:28:53.7 AS: Yeah. Exciting. Exciting. Well, Bill on behalf...
0:28:58.9 BB: It'll be on my tombstone, acceptability is not desirability.
0:29:01.7 AS: Yeah, exactly. We have accepted the death. It is acceptable. It's not desirable, but... On behalf of everyone at The Deming Institute, I want to thank you, Bill, for this discussion. Again, it's a fun one to hear what you're thinking about. And for listeners, remember to go to Deming.org to continue your journey. Any final thoughts Bill?
0:29:31.4 BB: Keep looking good Andrew, keep looking good.
0:29:34.0 AS: I wanna go beyond looking good. If you wanna keep in touch with Bill, just find him on LinkedIn. He responds. This is your host, Andrew Stotz, and I'll leave you with one of my favorite quotes from Dr. Deming. People are entitled to joy in work.
Więcej odcinków z kanału "In Their Own Words"
Nie przegap odcinka z kanału “In Their Own Words”! Subskrybuj bezpłatnie w aplikacji GetPodcast.