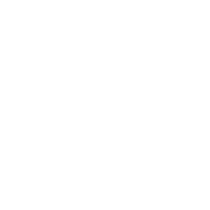
The Toyota Way: Responding to, Preventing and Learning from Mistakes with Jeff Liker
My guest for Episode #498 of the Lean Blog Interviews Podcast is Jeffrey K. Liker. Jeff is Professor Emeritus from the University of Michigan, President of Liker Lean Advisors, and author of the great books in the Toyota Way series.
Episode page with video, transcript, and more
He was previously a guest here in Episodes 3, 4, 37, 39, 41, 111, and 400.
Today, we have a discussion centered around learning from mistakes in the context of Toyota and lean methodologies. The episode delves into the significance of recognizing, reacting to, and learning from mistakes within organizations that employ Toyota Production System (TPS) or lean strategies. Jeff shares his insights on how Toyota's culture of continuous improvement and learning from errors fundamentally drives its success. The conversation touches on Toyota's approach to leadership and problem-solving, emphasizing the structured response to mistakes at different levels of the organization, from the factory floor to top management.
The episode further explores the Toyota leadership model, illustrating how leaders at various levels are expected to react when mistakes occur. Liker explains the role of the andon cord system in facilitating immediate problem identification and resolution, showcasing Toyota's commitment to quality and efficiency. He elaborates on the multi-layered leadership response to errors, detailing the responsibilities of team leaders, group leaders, and higher management in fostering a culture of learning and improvement. The discussion underscores the importance of a systemic approach to problem-solving, where the focus is on understanding and addressing the root causes of mistakes rather than attributing blame to individuals. This episode offers valuable insights into the principles of lean leadership and the critical role of acknowledging and learning from mistakes in achieving organizational excellence and innovation.
Questions, Notes, and Highlights:- How you'd expect Toyota leaders to react to a mistake on the factory floor?
- Less likely to blame an individual?
- Root cause vs. controllable cause?
- That can be a tough lesson to teach other companies?
- Hardest habit to break is the blame habit?
- Mistakes people make in trying to help change behavior
- What's necessary, in another company's workplace culture, for people to feel safe pulling the andon cord or speaking up?
- Article about the Ford plant and andon cords in 2007
- Jeff insights on that Dearborn plant
- The mention of psychological safety in “Toyota Culture”?
- What do you think of the phrase “psychological safety”? Or just the concept of it?
- Fujio Cho – biggest surprise was that TMMK workers were afraid to pull the andon cord
- New book: Engaging the Team at Zingerman's Mail Order
The podcast is brought to you by Stiles Associates, the premier executive search firm specializing in the placement of Lean Transformation executives. With a track record of success spanning over 30 years, it's been the trusted partner for the manufacturing, private equity, and healthcare sectors. Learn more.
This episode is also brought to you by “The Optimistic Outlook,” hosted by Barbara Humpton, CEO of Siemens USA. This podcast is a hub for those passionate about transformative concepts that shape both our workplaces and our world. Find it in your favorite podcast app.
This podcast is part of the #LeanCommunicators network.
Flere episoder fra "Lean Blog Interviews - Healthcare, Manufacturing, Business, and Leadership"
Gå ikke glip af nogen episoder af “Lean Blog Interviews - Healthcare, Manufacturing, Business, and Leadership” - abonnér på podcasten med gratisapp GetPodcast.