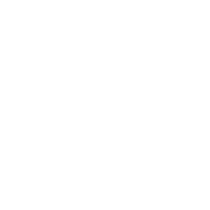
Josh Howell, LEI President, and Mark Reich, LEI Chief Engineer Strategy, join Olivier Larue, President of Ydatum, and discuss the Toyota Production System (TPS), the three elements embedded within TPS that make it more than just a production system, and the ability of TPS to foster problem-solving and creativity. Olivier worked with Mark at the Toyota Supplier Support Center (TSSC) in the late 1990s and has led Ydatum since 2000, assisting companies in implementing its version of TPS. Olivier recently authored the first of three volumes of The Toyota Economic System, which will present the three elements of the “Toyota triangle” — philosophical, technical, and managerial — and their necessity in making TPS an economic system for growth.
TPS has enabled mass production to accommodate customization, which had been minimized in the pursuit of lower costs for large quantities of standardized goods, says Olivier. TPS allows companies to “build a product affordably and very much customized to the desires of the customer, one without compromising the other.” Yet when attempting to apply TPS it remains difficult for many organizations to simultaneously achieve the primary goals of TPS — highest quality, lowest cost, and shortest lead time.
Josh and Mark explore with Olivier the importance of the Toyota triangle in achieving TPS goals, especially longer-term goals, and examine the relationship of the triangle to the better known TPS “house” (the roof of three goals, supported by jidoka and just-in-time columns, etc.). The house embodies philosophical, technical, and managerial elements throughout, notes Olivier, but they are not specifically called out in the house. Human development, also not shown in the house, is at the center of the Toyota triangle. Olivier says human development is critical because despite advances in artificial intelligence, currently only people can solve complex problems, human problems. “TPS at the end of the day is trying to solve a human problem using people through the human creativity and the human intelligence.”
Olivier also discusses the organizational problems he encounters with problem-solving. For example, he often sees people gravitating toward problems they know how to solve instead of solving the right problem. This occurs because it’s not always safe to solve the right problem and individuals don’t have the courage to take them on. “It’s very important for companies to realize that if they don’t provide an environment where it’s safe to solve problems, two things are going to happen: problems are not going to get solved, or if some problem gets solved it will be the wrong one... As management and leaders, you have to be able to encourage the people to solve difficult problems without fear of having negative consequences if they fail.”
Learn more about TPS and lean leadership at lean.org
More episodes from "WLEI - Lean Enterprise Institute's Podcast"
Don't miss an episode of “WLEI - Lean Enterprise Institute's Podcast” and subscribe to it in the GetPodcast app.